Multi-Purpose Box Oven
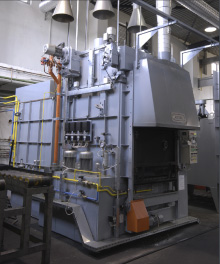
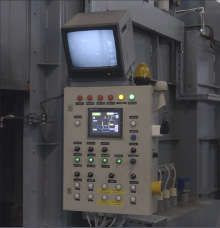
FEATURES
Heating Method: | electric resistance heating |
Power: | 140 kW |
Chamber Dimensions: | 900 x 650 x 1200 mm |
Max. Operating Temperature: | 1000 °C |
Temperature Accuracy in an Oven Chamber: | ± 5 °C |
Batch Weight: | 600 kg |
Thermal Insulation: | refractory fireclay lining |
Controls: | PLC, PC |
Data Logging: | PC, full documentation |
Application: | case hardening of gearbox parts |
DESCRIPTION
This is a fully gas-tight, directly heated box oven integrated with a cooling and hardening chamber. When the door is opened, the charge is loaded in a basket from the feed conveyor on the cooling chamber conveyor by a mechanical feeder. The external door is then closed and the cooling chamber is filled with a protective atmosphere. Then, the fire resistant door between the cooling chamber and the oven chamber opens, allowing the chain-belt conveyor (in the cooling chamber conveyor) to pass the charge from the lock chamber into the oven chamber. The charge is heated by radiant tubes or heating resistors in the oven, while the gas inside the oven is circulated by a fan in the oven top. On completion of the heating and diffusion cycles, the door opens again and the chain-belt conveyor pulls the charge back through the lock chamber onto an elevator platform in the cooling chamber. The elevator platform then descends, submerging the charge into a hardening fluid. The bottom part of the cooling chamber accommodates a hardening vat, allowing the hardening process to be performed without any exposure to the ambient atmosphere. An agitator is used to maintain a uniform temperature distribution in the hardening fluid. The cooling chamber can also be fitted with a circulation fan to cool the carburised parts without hardening while under a protective atmosphere. When cooled or hardened, the charge is unloaded by the chain-belt conveyor through the open door onto the external loading conveyor. It is possible to use a dual cooling chamber design that enables the next charge to be loaded into the oven, while the previous one is still being cooled, which increases oven capacity. It is a highly sophisticated piece of equipment that is capable of performing complex heat treatment processes, and can be fitted with various accessories to create a self-contained process line with excellent productivity. Accessories include a preparatory roller table, handling trolley, washer, pre-heating oven, tempering furnace and deep-freezing unit. The line can be manually operated or fully automatic.
APPLICATION
Sophisticated heat treatment of mass-produced steel products (components, machine parts, etc.) or the heat treatment of consecutive batches in the same oven but under different protective atmospheres (e.g. bright annealing, normalisation, case hardening, nitrocementation, etc.).
BUYING CRITERIA
Process objective, heat treating temperature and temperature accuracy, a time/temperature curve of the heat treating process, dimensions and weight of products, method of loading and unloading, the equipment required for loading and unloading, protective atmosphere requirements, heat treatment capacity requirement (kg/h), oven operating hours, heating method requirements (gas or electrical), etc.
Click here to download the product sheet (pdf)
For the latest version of the free Adobe Acrobat Reader® to view the pdf click here.
OUR MAIN ACTIVITIES
Our core business is the manufacture of industrial furnaces and thermal process equipment in accordance with the customer’s process specifications and technical requirements.
We provide troubleshooting, regular or occasional maintenance, as well as the renewal and upgrade of industrial furnaces.
Our company has gained a lot of experience in the construction of steel structures. We ourselves do minor cutting works, while, for doing large-scale ones, we cooperate with highly experienced professional companies.
We undertake the annealing and stress relieving heat treatment of large and heavy workpieces in the furnace.